It is all about saving time…
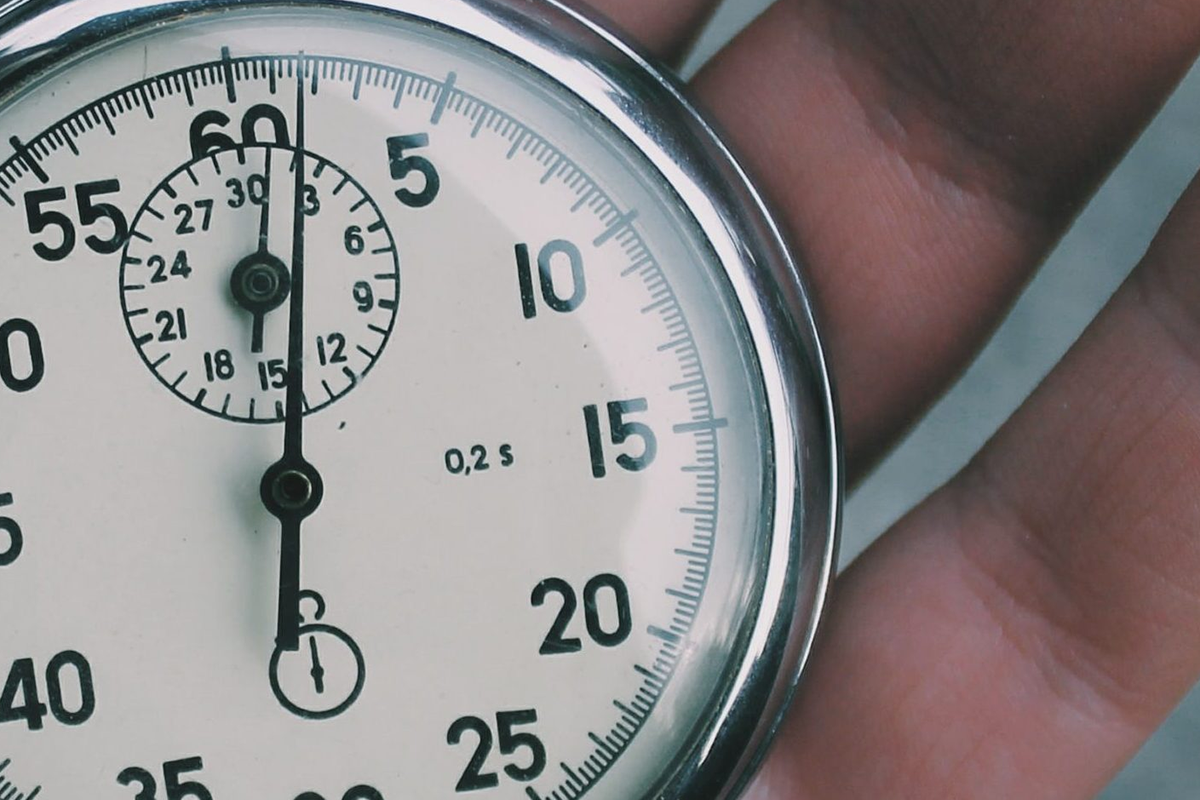
Everyone who deals with the implementation of lean management in business processes and corporate culture knows that the most important principle is to reduce waste from the customer’s point of view in all processes. Everyone knows the 7+1 types of waste, the acronym TIMWOODS and what it means. Both in the production environment and in the administrative processes. What they all have in common is that in 80% of all cases we reduce the time needed to execute processes. Because time is money!
One of the most popular and easiest to implement tools from the Lean Management Toolbox to reduce exactly these types of waste is the 5S method. When Toyota introduced the Toyota Production System (TPS) in the 1960s, the 5S method was the essential approach to standardizing tasks, reducing lead times and improving quality. Since then, hundreds of thousands of companies have begun their lean journey by adopting 5S.
Because the barrier to entry into the world of lean management tools is low with the 5S method, 5S has become widely accepted as an approach in this country, especially in industrial settings. This has been and continues to be a great success. Countless “5S games” have been played to train employees, and countless times audits have been conducted in areas of the company and the results compared month after month.
However, I have found that most companies that have adopted 5S as a tool to increase efficiency and quality in processes have not evolved the tool. (As an aside, this is even more at odds with the general Lean philosophy, which envisions an environment of continuous improvement.) The good news is that it’s not that hard to take the next steps to evolve this approach.
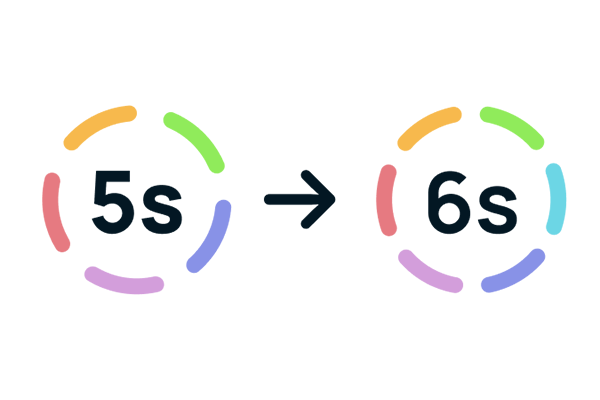
Make it 6S!
A first step is to add “safety” as a sixth “S.” The advantage here is obvious. Instead of conducting regular and independent safety audits, simply include this part in the 5S audits – in other words, make it 6S! This approach will save you time and still not lose focus. I still have the words of one of my lean management mentors in mind. He said in the early 2010s that if you introduce and implement 5S properly, you get the sixth “S” for free. That’s basically true, too. Structured and clean workplaces have a higher safety standard per se. It is all the more obvious that you can easily integrate this aspect into your 5S concept.
Time studies have shown that if you integrate safety into the 5S standard, you can save about 2-6 hours per month, depending on the scope and size of the areas, and still keep the focus on safety. If this approach is then digitized, you can save up to 50% time per audit performed.
With the GoLeanSigma Lean Management Toolbox, you can leverage these efficiencies today. So when will you start to increase your efficiency in lean management?